Waste Plastic Pyrolysis Plant Is Beyond Design, Towards Sustainability
- icholsy
- Dec 27, 2023
- 2 min read
Engineering Marvel: Unraveling the Pyrolysis Process
At the core of the waste plastic pyrolysis plant design lies the profound understanding of the pyrolysis process. Pyrolysis, an intricate thermochemical decomposition of organic materials in the absence of oxygen, propels the transformation of waste plastics into valuable byproducts. This ingenious method not only mitigates the environmental burden of plastic waste but also extracts economic value from what was once considered a pollutant.
The plant incorporates a meticulously crafted reactor vessel where the magic of pyrolysis unfolds. The reactor's design facilitates controlled heating and anaerobic conditions, ensuring the optimal conversion of complex hydrocarbons within plastic polymers into valuable outputs.
Structural Elegance: Navigating the Reactor Dynamics
The reactor, a crucible of innovation in the waste plastic pyrolysis plant design, is crafted with precision. Its structural integrity, paramount for the safety and efficiency of the process, involves a robust combination of refractory materials and heat-resistant alloys. This synergy enables the reactor to withstand the intense thermal and chemical stresses inherent in the pyrolysis journey.
Furthermore, the reactor design incorporates a sophisticated heat exchange system, a labyrinth of tubes and chambers strategically positioned to maximize thermal efficiency. This intricate arrangement not only conserves energy but also ensures a seamless transfer of heat throughout the pyrolytic conversion, optimizing resource utilization.
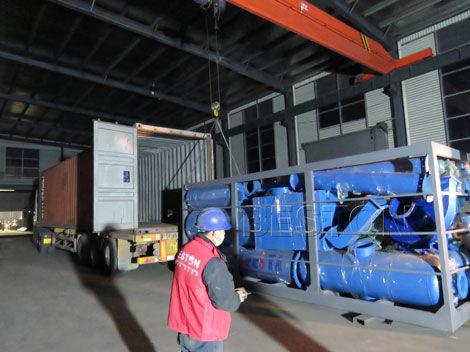
Process Optimization: Balancing Act in Waste Plastic Pyrolysis
The hallmark of a well-crafted waste plastic pyrolysis plant lies in its ability to strike a delicate balance between throughput and product quality. This involves a meticulous consideration of factors such as feedstock composition, temperature profiles, and residence times within the reactor.
The design intricacies extend to the condensation system, an indispensable component in capturing the spectrum of pyrolytic byproducts. Here, a cascade of condensers and separators work in tandem, each calibrated to capture specific fractions of the pyrolytic output. This nuanced approach allows for the extraction of diverse products, including liquid fuels, gases, and carbonaceous residues.
Environmental Imperative: Emission Control Mechanisms
An authoritative waste plastic pyrolysis plant design is incomplete without a robust emission control strategy. To mitigate environmental concerns, the design incorporates cutting-edge gas treatment systems. These systems, often involving catalytic converters and scrubbers, ensure that any residual emissions are meticulously treated before release, adhering to stringent environmental standards.
Technological Finesse: Automation and Control Systems
In the realm of advanced waste management, technology reigns supreme. The waste plastic pyrolysis plant design embraces the digital era with state-of-the-art automation and control systems. These systems, governed by intricate algorithms, orchestrate the entire pyrolysis process with unparalleled precision. From regulating temperature gradients to optimizing feedstock flow, technological finesse ensures operational efficiency and product consistency.
Commenti